Understanding M1 Manufacturing Software: Features & Benefits
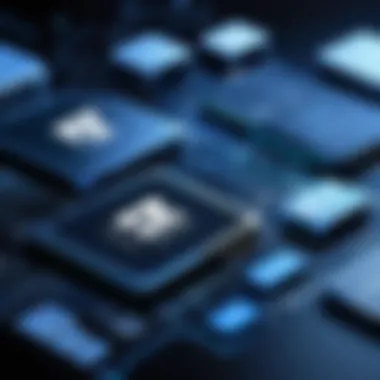
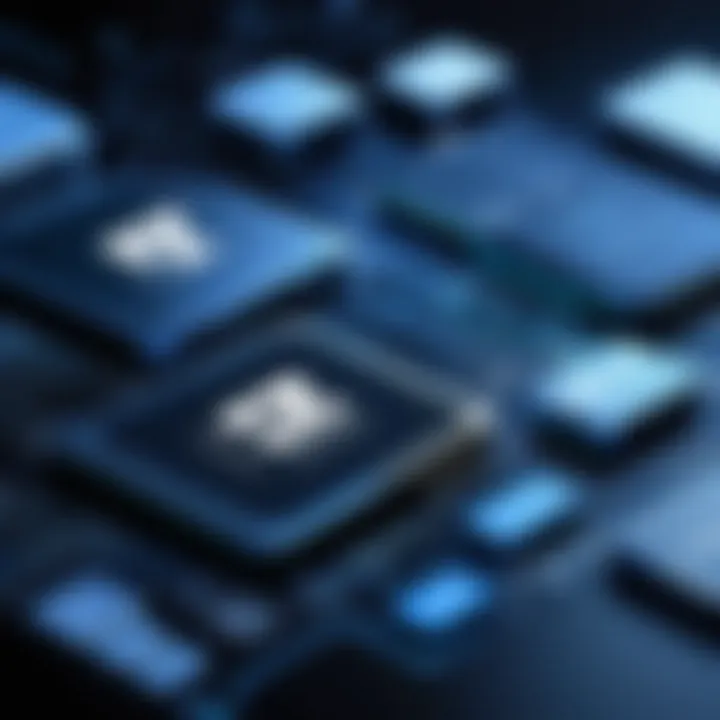
Intro
The manufacturing landscape has seen transformative changes in recent years, driven largely by the integration of advanced software solutions. One such software is M1 manufacturing software, which stands at the forefront of this evolution. Designed to optimize various production processes, M1 promises to enhance both efficiency and productivity. This article seeks to guide the reader through the intricate workings of M1, breaking down its capabilities, performance metrics, and overall impact on manufacturing operations.
Features and Capabilities
M1 manufacturing software is equipped with various features that cater to the needs of manufacturers. Understanding these features can help professionals make informed decisions about its implementation and application.
Overview of Key Features
M1 showcases a comprehensive set of functionalities that streamline operations. Some notable features include:
- Inventory Management: M1 provides real-time tracking of inventory levels, helping businesses maintain optimal stock without over-ordering.
- Job Scheduling: The software allows for effective planning of job schedules, thereby minimizing delays in production.
- Cost Tracking: This feature enables businesses to monitor production costs closely, supporting better financial decisions.
- Reporting and Analytics: M1 offers robust reporting tools that provide insights into operational performance, facilitating data-driven strategies.
User Interface and Experience
The user interface of M1 is designed with accessibility in mind. Important aspects include:
- Intuitive Design: Users often find the layout easy to navigate. It reduces the learning curve, allowing new users to adapt quickly.
- Customizable Dashboards: The ability to personalize dashboards helps users focus on the most relevant data for their specific role, enhancing productivity.
Performance and Reliability
When evaluating software, performance and reliability are critical factors for manufacturers. M1 excels in both these areas, providing a solid foundation for operational success.
Speed and Efficiency
M1 is designed to process large amounts of data swiftly. Users appreciate the quick response times, which can result in substantial time savings during daily operations. Reports can be generated in moments, allowing managers to make timely decisions.
Downtime and Support
M1 is built with redundancy and support in mind.
- Minimal Downtime: The software is known for its reliability, which translates into reduced downtimes during critical operation periods.
- Customer Support: Users can access a dedicated support team for assistance, ensuring that any challenges can be resolved swiftly.
"M1 manufacturing software is revolutionizing how we view production efficiency, demonstrating that technology's integration into manufacturing is not just beneficial; it is essential."
M1's various elements combine to create a powerful tool for manufacturers. Its extensive feature set, solid performance, and user-centric design make it an invaluable asset in modern manufacturing environments.
Preface to M1 Manufacturing Software
M1 Manufacturing Software represents a crucial element in the landscape of modern production. As industries grow increasingly complex and competitive, the need for software that can efficiently manage manufacturing processes becomes paramount. This section serves to clarify the significance of M1 software within this context, shedding light on its inherent advantages and considerations for implementation.
Importance of M1 Manufacturing Software
M1 Manufacturing Software is designed to optimize manufacturing operations. With its array of features, it helps organizations streamline workflows, manage production schedules, and reduce waste. This efficiency is essential in meeting consumer demands while keeping costs under control.
Key benefits of utilizing M1 software include:
- Increased Productivity: M1 software automates repetitive tasks, which allows employees to focus on high-value activities.
- Real-time Data Access: Users can make decisions based on current information, improving responsiveness to market changes.
- Enhanced Collaboration: The software facilitates communication between departments, breaking down silos and ensuring better alignment on production goals.
- Flexibility and Scalability: Businesses can adapt the software to their specific needs and scale it as they grow, ensuring continued relevance.
M1 software also considers user-friendliness. A well-designed interface can reduce the learning curve for new users, making adoption smoother and enhancing overall staff satisfaction.
Additionally, by leveraging M1 Manufacturing Software, organizations position themselves for long-term success. They can respond effectively to industry changes, integrating new technologies such as Artificial Intelligence in the future.
"M1 Manufacturing Software is not just a tool but a strategic asset that shapes operational efficiency in the manufacturing realm."
In summary, the importance of M1 Manufacturing Software cannot be overstated. Its relevance stretches across various facets of operation, providing significant benefits that can empower companies within the manufacturing sector. As we proceed through this article, we will delve deeper into the evolution, features, benefits, and challenges associated with M1, offering you a comprehensive view of this impactful technology.
The Evolution of Manufacturing Software
The development of manufacturing software has drastically transformed operational landscapes over the decades. This evolution can be traced back to the infancy of computer technology, where manual processes dominated. Early systems laid a foundation which M1 software builds upon today. Understanding this progression is essential to grasp how tools like M1 are not just advanced versions of their predecessors but are instead integral to competitive advantage in contemporary manufacturing environments.
Historical Context
The roots of manufacturing software can be found in the 1960s and 1970s, as businesses started adopting computers for basic data processing. Initially, these systems were primarily focused on accounting and inventory management. The introduction of Material Requirements Planning (MRP) marked a pivotal shift. It allowed companies to optimize materials management and production scheduling.
As industries began to see the benefits of automation, the 1980s brought forth more sophisticated systems, namely MRP II, which integrated financial and production planning. This era saw the conception of integrated software solutions that streamlined and interconnected various business functions.
Transitioning into the 1990s, the concept of Enterprise Resource Planning (ERP) emerged. This represented another leap forward. It combined the features of MRP and MRP II but expanded them, incorporating broader business processes and enabling organizations to operate more cohesively.
Technological Advances
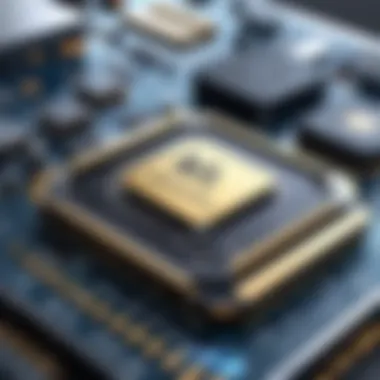
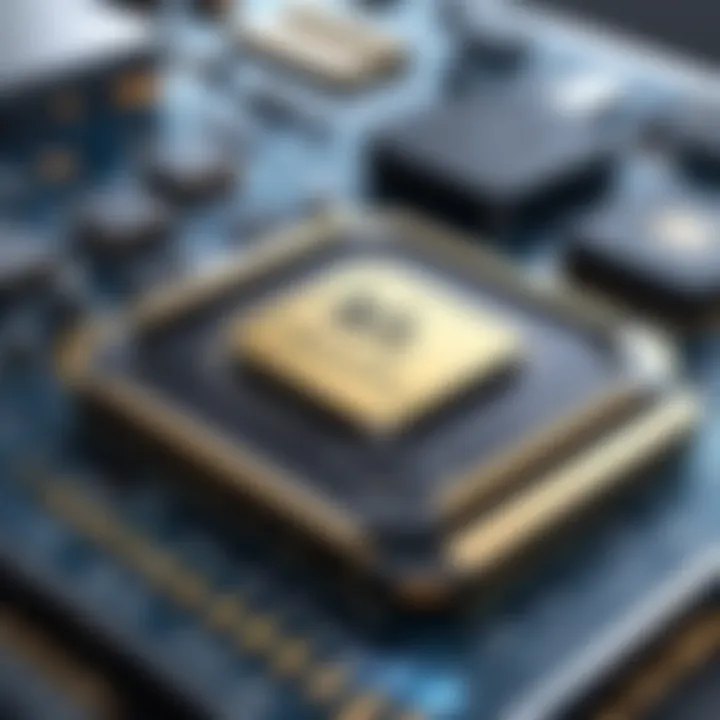
The 21st century heralded an era of rapid technological advances. The advent of the Internet and cloud computing facilitated real-time data accessibility and collaboration across geographies. Manufacturing software became more than just an internal tool; it evolved into a platform that promotes connectivity between various stakeholders, including suppliers and customers.
Key technological advances have also included:
- Automation and Robotics: Automation has redefined productivity metrics, allowing for tasks once thought to require human intervention to be optimized and executed by machines. Software like M1 seamlessly integrates with automation strategies.
- Big Data Analytics: The ability to collect and analyze massive data sets has led to more informed decision-making. M1 software harnesses these analytical capabilities to provide insights that were previously unattainable.
- Artificial Intelligence: Integrating AI has enhanced the capabilities of manufacturing software, allowing for predictive maintenance and improved demand forecasting. This revolutionized user interaction with the technology, leading to more intuitive experiences.
These advances illustrate the dynamic nature of manufacturing software, specifically M1, which continues to adapt and respond to technological trends, addressing industry needs more effectively than ever before.
"The evolution of manufacturing software is a testament to the significant role technology plays in advancing operational efficiency and strategic decision-making."
This narrative highlights not only the historical aspects but also the technological advancements that have influenced current manufacturing software systems, cementing their necessity in a highly competitive market space.
Core Features of M1 Software
The core features of M1 manufacturing software are crucial for understanding how this tool can enhance operational performance within various manufacturing environments. These features are designed not only to optimize processes but also to drive efficiency across the board. In this section, we will analyze three predominant aspects: Production Planning and Scheduling, Inventory Management, and Quality Control Mechanisms. Each of these features plays a significant role in streamlining operations and enhancing overall productivity.
Production Planning and Scheduling
Production planning and scheduling form the backbone of any effective manufacturing process. M1 software excels in enabling businesses to create efficient production schedules based on real-time data. This functionality allows manufacturers to allocate resources optimally, minimize idle time, and adapt to unforeseen changes rapidly.
A comprehensive view of production timelines can be achieved with this software. It permits the simulation of various production scenarios, thereby empowering managers to make informed decisions. Some key benefits include:
- Resource Allocation: M1 accurately forecasts the resources needed for production, ensuring that materials and labor are always available when required.
- Lead Time Reduction: By creating precise schedules, M1 minimizes the lead time, thereby enhancing customer satisfaction and meeting delivery deadlines.
- Flexibility: Changes in demand can be handled promptly, enabling manufacturers to pivot as necessary to maintain operational flow.
Inventory Management
Effective inventory management is critical to running a successful manufacturing operation. M1 offers tools that facilitate tracking of inventory levels, order processing, and demand forecasting, thus ensuring that stock levels meet production needs without incurring excessive holding costs.
One of the notable capabilities of M1 is its integration with suppliers and distributors. This connection allows for more efficient reordering processes and improves supply chain management. Key points of interest include:
- Real-Time Tracking: Users can monitor inventory in real-time, which reduces the chances of stockouts or overstock situations.
- Automated Replenishment: The software can automate reorder processes based on predefined thresholds, ensuring materials are always on hand.
- Reporting and Analytics: M1 provides detailed reports on inventory turnover and trends, enabling better decision-making.
Quality Control Mechanisms
Quality control is an indispensable aspect of manufacturing that directly affects product reliability and customer satisfaction. M1 manufacturing software incorporates robust quality control mechanisms that assist in maintaining high standards for products.
These mechanisms provide users with the tools to establish quality benchmarks and perform systematic inspections and tests. M1 facilitates:
- Data Collection: Automated data collection from the production line ensures accuracy in monitoring quality issues as they arise.
- Defect Tracking: The software enables manufacturers to trace defects back to their origin, making it easier to remedy problems and prevent recurrence.
- Compliance Management: M1 helps ensure that manufacturing practices comply with industry standards, reducing the risk of non-compliance penalties.
Effective quality control can lead to significant gains in market reputation and customer loyalty.
Benefits of M1 Manufacturing Software
The benefits of M1 Manufacturing Software are crucial in the context of modern manufacturing. It enhances operational capabilities in several key areas. Understanding these benefits helps businesses optimize their processes. This includes improved productivity, cost efficiency, and informed decision-making. The software plays a vital role in streamlining workflows, making it essential for contemporary manufacturing environments.
Enhanced Efficiency
Enhanced efficiency is one of the most significant benefits of M1 Software. It facilitates streamlined production processes which contribute to better resource management. By enabling real-time monitoring and adjustments, manufacturers can significantly reduce downtimes.
M1 Software provides tools for tracking production metrics, identifying bottlenecks, and reallocating resources swiftly. This agility allows for a more responsive manufacturing process, which can adapt to changes in demand without a substantial lag.
- Key aspects of enhanced efficiency include:
- Automation of repetitive tasks
- Improved workflow management
- Reduced operational delays
These features help to maximize productivity, which is often a critical measure in manufacturing success.
Cost Reduction Strategies
Cost reduction is a prevailing concern in manufacturing, and M1 Software addresses this effectively. By optimizing processes, the software can lead to notable reductions in operational costs.
For instance, M1 allows for better inventory management. It prevents overproduction and minimizes excess inventories. This directly translates into lower storage costs and less financial tied up in unsold products. Moreover, with its advanced data analytics, companies can forecast demand more accurately leading to lower wastage.
- Important cost reduction strategies include:
- Streamlining supply chain operations
- Automating expense tracking
- Implementing predictive maintenance to reduce downtime costs
Overall, these strategies enhance profit margins and positively impact the bottom line.
Decision-Making Support
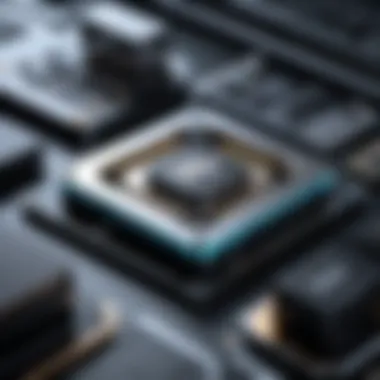
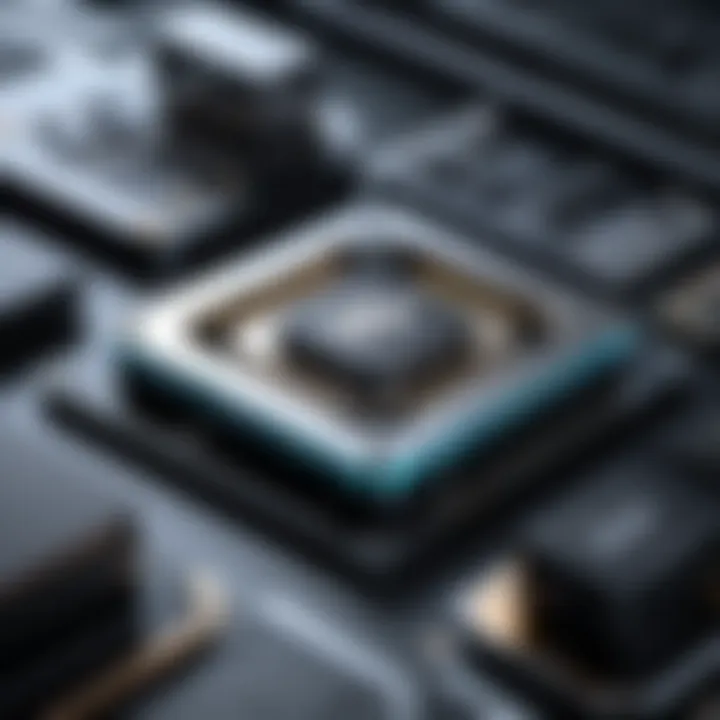
M1 Manufacturing Software also provides robust decision-making support. Access to precise data is crucial for informed decisions. The software aggregates data across all production levels and presents it in a user-friendly format. This empowers managers and stakeholders to analyze performance metrics effectively.
M1's reporting tools help in generating necessary insights for strategic planning. This facilitates a proactive rather than reactive approach in operations. Incorporating analytics in the decision-making process can lead to improvements in:
- Resource allocation
- Production scheduling
- Quality assurance strategies
User Experience and Interface Design
User Experience (UX) and interface design are central to the successful implementation of M1 manufacturing software. A well-crafted user interface not only enhances usability but is also vital for optimizing productivity in manufacturing processes. Given that M1 software is widely used across various sectors, integrating a user-friendly design can significantly impact the efficiency of operations.
Usability Assessment
To examine the effectiveness of the M1 software, a usability assessment becomes essential. This assessment focuses on several key factors:
- Ease of navigation: Users must be able to easily move through various sections of the software without unnecessary delays.
- Intuitive design: The layout of functions and features should resonate with the users’ expectations, reducing the learning curve.
- Accessibility: The software must accommodate different user abilities, ensuring that everyone can work efficiently with it.
Efficient usability assessment not only identifies current strengths but also highlights areas needing improvement. It can be conducted through user testing and feedback, enabling businesses to tailor the software more precisely to their needs. Furthermore, regular assessments ensure the software evolves alongside user demands.
Training and Support Resources
Proper training and support resources are critical for enhancing user experience in M1 software. Providing users with comprehensive training ensures that they understand the software's full capabilities. Key elements to consider include:
- Structured training sessions: Organizing live webinars or interactive sessions can greatly enhance understanding.
- Online tutorials and documentation: Having readily available resources allows users to learn at their own pace.
- Support forums: Establishing a community where users can share tips and solve each other’s problems fosters collaboration.
Regular updates to training content ensure that users remain informed about new features or changes in the software. Support resources are equally important, as they provide immediate assistance to users facing challenges during operation.
Through effective training and support, organizations can ensure that their teams make the most out of M1 software, ultimately driving better outcomes in manufacturing processes.
Integration with Other Software Solutions
The integration of M1 manufacturing software with other software solutions is crucial for enhancing operational efficiency and streamlining business processes. In modern manufacturing environments, organizations deal with a variety of software systems, including Enterprise Resource Planning (ERP), Customer Relationship Management (CRM), and other specialized tools. Achieving seamless integration among these software applications can lead to improved data flow, reduced redundancy, and better decision-making capabilities.
ERP System Compatibility
ERP systems are designed to consolidate business functions into a unified framework. M1 manufacturing software's compatibility with ERP systems allows companies to automate and synchronize their operations. For instance, when production schedules change in M1, updates can be reflected in the ERP system without manual data entry, minimizing errors and saving time. This compatibility often results in:
- Real-time data visibility: Stakeholders can access accurate information regarding inventory levels, production status, and financial metrics without delay.
- Streamlined processes: Automated workflows reduce the chances of miscommunication between departments, which enhances overall productivity.
- Informed decision-making: With better visibility into operations, managers can make faster and more effective decisions based on comprehensive data.
Data Exchange Protocols
Data exchange protocols are fundamental in ensuring that different systems can communicate effectively. These protocols define the standards used for data transfer among software applications. M1 manufacturing software utilizes various industry-standard protocols, which facilitate secure and efficient data exchange. Key points about data exchange protocols include:
- Interoperability: M1's ability to work with different data formats and systems ensures that companies can integrate their existing software without overhauling their entire infrastructure.
- Scalability: As organizations grow, the requirement for integrating new tools becomes essential. M1 supports various protocols, making it adaptable to future changes.
- Data Integrity: Established protocols ensure that the quality and accuracy of the data exchanged remain intact, which is critical for maintaining operational efficiency and reliability.
Effective integration capacities of M1 software empower manufacturers to adapt swiftly to market changes and improve competitive advantage.
Understanding the importance of integration in M1 software helps organizations leverage their existing investments and develop a cohesive ecosystem that supports robust manufacturing processes. It ensures both current and future technological needs are met, positioning firms for sustained growth.
Industry Applications of M1 Software
The M1 manufacturing software plays a pivotal role across various sectors in the manufacturing industry. Its utility extends far beyond basic production tasks by enabling a comprehensive suite of functionalities tailored to meet the specific needs of different manufacturing environments. Understanding these applications is crucial for stakeholders aiming to leverage technology for optimizing their operations.
Manufacturing Sectors
M1 manufacturing software caters to several sectors within manufacturing. Here are some of the main fields that benefit significantly from its powerful capabilities:
- Aerospace and Defense: In these sectors, quality and precision are paramount. M1 software helps manage complex supply chains and ensures compliance with strict regulatory requirements. It aids in tracking parts and materials, which enhances traceability.
- Automotive: The automotive industry is characterized by fast-paced production and high-volume requirements. M1 allows for dynamic production scheduling, which minimizes delays and fosters lean manufacturing processes. Furthermore, it supports just-in-time inventory management, reducing storage costs and waste.
- Electronics: This sector demands continuous innovation and quick turnaround of new designs. M1 software incorporates flexibility in production planning, allowing manufacturers to adjust quickly to changes in consumer demand or technology.
- Consumer Goods: In the fast-moving consumer goods sector, responsiveness is essential. M1 assists manufacturers in managing inventory more effectively, ensuring stock levels meet fluctuating market demands without leading to excess.
- Medical Devices: Compliance with health regulations is vital in this field. M1 helps organizations implement quality control processes that are crucial in the production of medical devices, ensuring that all products meet safety standards.
This diversity in manufacturing applications showcases M1 software's adaptability and effectiveness. The software's ability to cater to the unique challenges faced in each sector emphasizes its relevance in modern manufacturing.
Case Studies
To better understand the impact of M1 manufacturing software, examining real-world applications provides valuable insights. Here are some illustrative case studies that indicate how various companies have benefitted:
- Aerospace Manufacturer: A leading aerospace manufacturer implemented M1 to streamline its production processes. The results included a 20% reduction in lead time and improved compliance with regulatory standards. The implementation led to better inventory management, reducing overhead costs significantly.
- Automotive Parts Supplier: An automotive parts supplier used M1 to enhance its production scheduling. By harmonizing production flows and inventory levels, the company noted a 15% increase in on-time deliveries. The result was improved client satisfaction and stronger market positioning.
- Electronics Assembly Firm: This firm integrated M1 to manage varying production demands. Due to faster adaptation to changes in order volumes, they saw a reduction in production bottlenecks. Additionally, the visibility provided by M1 facilitated better resource allocation.
- Medical Device Company: A medical device manufacturer employed M1 for strict quality control processes. Post-implementation, the company reported a decrease in compliance-related issues and enhanced operational efficiency. The software enabled timely updates to processes and documentation, aligned with evolving regulations.
These case studies illustrate how M1 manufacturing software effectively addresses specific challenges and drives efficiency and compliance across diverse manufacturing sectors. The positive outcomes suggest a significant return on investment and an enhanced competitive position in the market, solidifying M1's role as an essential tool in contemporary manufacturing environments.
Challenges and Limitations
Understanding the challenges and limitations of M1 manufacturing software is crucial for organizations considering its implementation. This section highlights key barriers and ongoing maintenance needs, which can significantly affect users' experience and the overall effectiveness of the software.
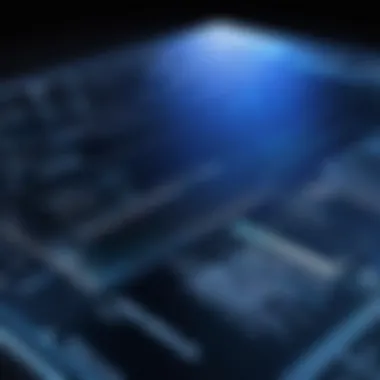
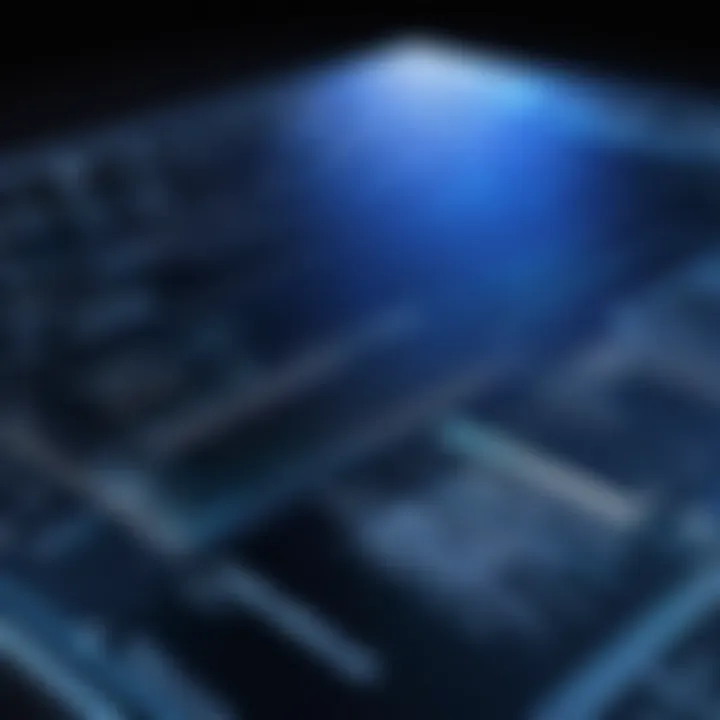
Implementation Barriers
Implementing M1 manufacturing software often encounters several barriers that can hinder a smooth transition. One primary challenge is the resistance to change among employees, who may be accustomed to existing processes and systems. This resistance can slow down the adoption of new tools, leading to disruptions in productivity.
Moreover, integration with other systems, such as Enterprise Resource Planning (ERP) software, can be complex. Organizations must ensure that the M1 software works effectively with existing infrastructure, which may require significant technical expertise. Additionally, data migration, which involves transferring data from old systems to M1, can present risks of data loss or corruption if not executed carefully.
Financial investment is another critical factor. The costs associated with acquiring M1 software, customizing it to meet specific needs, and training staff can be substantial. Organizations should weigh these costs against the expected benefits, as the financial burden can delay or even prevent implementation.
Ongoing Maintenance Needs
Once M1 manufacturing software is operational, regular maintenance is necessary to sustain its performance. Continuous software updates are essential to enhance functionality and security. Failure to apply these updates can leave the system vulnerable to breaches or bugs, which can disrupt operations.
Additionally, technical support is vital. Users may encounter issues that require assistance from IT staff or external support services. Ensuring that resources are available for troubleshooting can be a challenge, particularly for smaller firms with limited IT capabilities.
Companies must also ensure that staff receive ongoing training. As the software evolves, users need to stay updated on new features and functionalities. Lack of adequate training can lead to misuse of the software, reducing efficiency and productivity over time.
Future Trends in Manufacturing Software
In the age of rapid technological advancement, understanding future trends in manufacturing software is critical. The integration of sophisticated tools like M1 manufacturing software can redefine operational strategies. It can enhance productivity, streamline processes, and create smarter manufacturing environments. A forward-thinking approach can maximize benefits and mitigate potential challenges.
Artificial Intelligence Integration
Artificial Intelligence (AI) integration in manufacturing software presents transformative opportunities. Companies can leverage machine learning algorithms to analyze vast amounts of data. This results in informed predictive analytics regarding production outcomes, demand forecasting, and quality management. AI can automate repetitive tasks, allowing employees to focus on more strategic projects. It can also facilitate real-time data analysis, thus enabling quick decision-making.
For example, M1 software can be enhanced with AI-driven features that monitor production lines. If deviations or inefficiencies arise, the system can automatically adjust parameters to optimize workflow. This minimizes human error and significantly improves efficiency.
The consideration of AI in manufacturing software also extends to workforce management. By analyzing patterns in labor usage and capabilities, organizations can optimize their staffing plans. Consequently, resource allocation becomes more strategic and effective, helping to maintain operational efficiency even during peak demand.
Cloud Computing Impact
Cloud computing is another significant trend reshaping the landscape of manufacturing software. With its potential for reducing IT costs and improving accessibility, cloud services empower companies to manage their operations from anywhere in the world. M1 manufacturing software's move to cloud-based architecture enables continuous updates and real-time data sharing.
Cloud platforms provide the flexibility and scalability that modern manufacturers need. Businesses can adjust their storage and computing resources based on their specific needs. Further, collaboration improves as teams can access the same data simultaneously, regardless of location.
Importantly, cloud solutions often come with robust security measures. This alleviates concerns about data breaches in an era where cybersecurity is paramount. These capabilities make cloud integration an attractive option for manufacturers looking to innovate and grow.
Epilogue
In this article, we explored the evolving landscape of M1 manufacturing software. The concluding section serves a critical role in summing up the comprehensive insights discussed throughout the article. Understanding the importance of M1 software goes beyond merely recognizing its features; it encapsulates the real-world implications on modern manufacturing processes.
The primary takeaway is that M1 manufacturing software is fundamentally designed to optimize operations. It supports a variety of functions that are crucial for businesses aiming for greater efficiency and productivity. Improved production scheduling, effective inventory management, and robust quality control are just a few elements that showcase its utility. These features collectively lead to enhanced operational efficiency.
Benefits of M1 implementation are also significant. By adopting this software, companies can realize substantial cost savings and make informed decisions based on accurate data analytics. Such capabilities can transform operational workflows and give a competitive edge to firms in the manufacturing sector.
"The role of M1 manufacturing software cannot be overstated in an industry facing continuous technological advancements and competitive pressures."
Furthermore, the considerations while implementing M1 software are crucial. Companies must evaluate their specific needs and the potential barriers such as integration challenges or training requirements. Ensuring proper support and training resources plays an essential role in facilitating a smooth transition.
Importance of References
References provide a link to additional information that can be beneficial for both new and experienced users. They offer detailed insights into technical specifications, user experiences, and industry applications of M1 software. Given the intricacies in the manufacturing sector, having access to carefully curated references is paramount. It ensures that users can delve deeper into specific aspects of the software and understand its implications in various contexts.
Benefits of Using References
- Enhanced Credibility: Citing recognized sources, such as academic journals or reputable industry reports, adds weight to the claims made about M1 software's capabilities and effectiveness.
- Informed Decision-Making: References assist professionals and IT experts in making better choices regarding software selection, implementation, and integration strategies.
- Continued Learning: As technology continually evolves, references help users stay updated with emerging trends and advancements within M1 and the broader manufacturing sector. This is especially important for developers and IT professionals, as they often need to adapt to new tools and environments.
- Comprehensive Understanding: For students or newcomers to the field, references provide a foundational understanding that can frame the use of M1 software in practical scenarios.
Considerations About References
While references are beneficial, it is crucial to assess their quality. Trustworthy resources will typically undergo thorough vetting processes and will provide current insights. Users should be cautious of outdated or unreliable references, as they can lead to misinformed actions.
"Quality references empower professionals to maximize the potential of M1 manufacturing software, fostering not only organizational growth but also personal development within the field."
Further Reading
The concept of further reading plays a crucial role in enhancing the knowledge base of readers interested in M1 manufacturing software and its overarching implications in modern manufacturing. This segment encourages delving beyond the fundamentals, providing readers with avenues to explore related subjects that augment their understanding. In today's fast-evolving technological landscape, grasping the nuances of M1 software necessitates not only an understanding of its current applications but also its potential future developments.
Importance of Further Reading
- Deepening Knowledge: Further reading offers opportunities for practitioners and students to deepen their comprehension of specific areas, such as artificial intelligence or cloud computing's effect on manufacturing software. These insights can be vital for informed decision-making in their professional undertakings.
- Understanding Context: Contextual knowledge can significantly enhance one's understanding of how M1 software fits into broader industry trends. Readers may find information on historical evolution and technological advancements that set the stage for modern software innovations.
- Exploring Best Practices: Engaging with further literature can lead to discovering best practices for implementing software solutions effectively. This understanding is essential for ensuring that users leverage M1's capabilities fully and avoid common pitfalls.
Considerations About Further Reading
- Quality of Sources: It's pivotal to choose reputable sources. Peer-reviewed journals, industry reports, and renowned publications like Britannica or Wikipedia can provide accurate and reliable information.
- Relevance to Current Trends: Selecting resources that reflect current industry trends will keep readers updated and prepared for new developments in manufacturing software.
- Interdisciplinary Approach: Readers are encouraged to look beyond manufacturing alone. Insights from related fields, such as information technology or operational management, can provide valuable perspectives on optimizing the usage of M1 software.
"Education is the most powerful weapon which you can use to change the world." – Nelson Mandela
Closure
In summary, integrating further reading into training and learning pathways enables software developers and IT professionals to stay current and knowledgeable. As they delve into M1 manufacturing software and the associated fields, they can better prepare to navigate the challenges and opportunities that arise in the manufacturing sector.