Activating Inventory: Strategies for Success
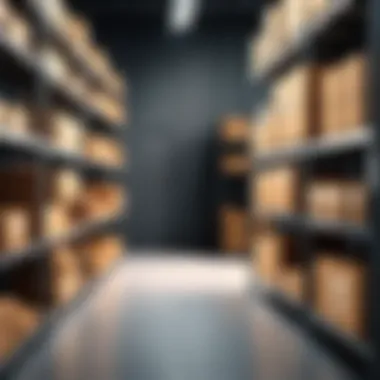
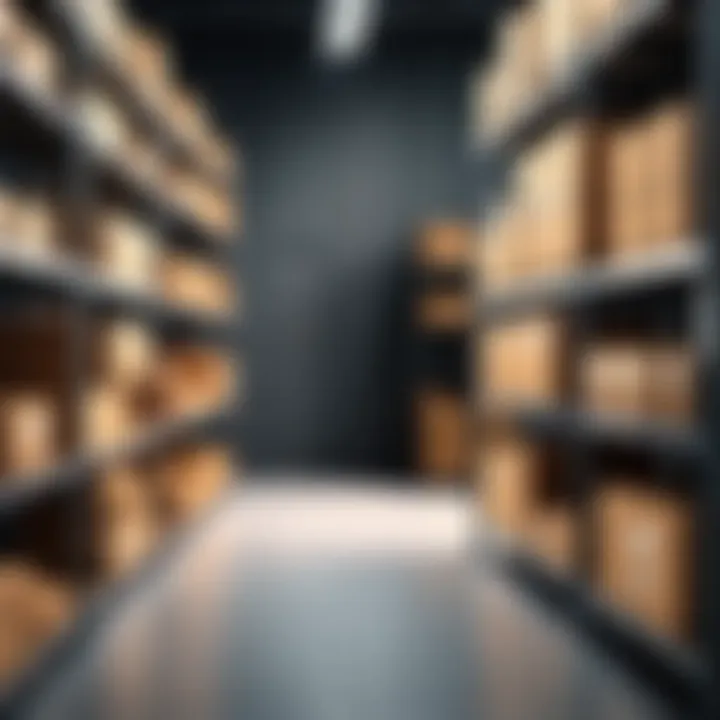
Intro
Activating inventory is a critical aspect of inventory management. It involves not only the management of stock levels but also the optimization of these levels to enhance operational efficiency and profitability. This guide aims to provide a deep dive into the world of inventory activation, highlighting key strategies, tools, and metrics that can improve stock efficiency and drive profitability.
Through understanding the essential components of inventory management, readers can gain insightful perspectives on how to make informed decisions. This is crucial for those looking to improve their inventory practices whether they are business owners, IT professionals, or students keen on learning about the field.
We will explore how technology plays a pivotal role in optimizing inventory workflows, guiding professionals to better manage their stock and resources.
Features and Capabilities
Overview of Key Features
To effectively activate inventory, one must be aware of the key features necessary for efficient inventory management. Features such as real-time tracking, automated reordering, and comprehensive reporting contribute directly to improved decision-making processes and stock management.
- Real-Time Tracking: This facilitates monitoring of inventory levels at any moment. It helps identify trends and reduces stock discrepancies.
- Automated Reordering: This minimizes human error and ensures that stock is replenished before it runs out, thus preventing potential sales losses.
- Comprehensive Reporting: Detailed reports shed light on stock performance and sales patterns. These insights aid in strategic planning and forecasting.
User Interface and Experience
A user-friendly interface is crucial for any inventory management system. A well-designed interface allows users to navigate quickly through essential features without overwhelming them. Here are some key considerations:
- Simplified Navigation: Clear menus and categories make finding information faster.
- Data Visualization: Easy-to-read graphs and charts enhance the understanding of inventory dynamics.
- Customization Options: Users should have the ability to tailor the interface to their unique needs, leading to a more personalized experience.
Performance and Reliability
Speed and Efficiency
Performance metrics are vital in determining the effectiveness of inventory activation strategies. Fast processing times, quick data retrieval, and efficient stock movement contribute to high operational efficiency. Delays can lead to reduced customer satisfaction and financial losses.
Downtime and Support
Reliability is a key factor in inventory management systems. Minimizing downtime is critical for maintaining smooth operations. Systems must also offer robust support to resolve any issues that may arise. The following aspects are important to consider:
- Regular Maintenance: Frequent updates and checks can prevent system failures.
- Responsive Support: Quick access to technical support can ensure that any challenges are addressed promptly.
"Activating inventory is not just about keeping stock. Itโs about creating a strategy that aligns with business goals to optimize resources and maximize profit."
This article will continue to explore powerful strategies and best practices in activating inventory, helping professionals in IT and related fields master their inventory management skills, ensuring they remain competitive in todayโs fast-paced market.
Understanding Inventory Activation
Inventory activation is a central concept in inventory management. It involves optimizing stock levels to enhance operational efficiency and increase profitability. Understanding how to properly activate inventory is crucial for any business that relies on physical goods. It goes beyond merely managing stock; it is about strategically managing inventory to meet customer demand while minimizing costs.
Definition of Inventory Activation
Inventory activation can be defined as the process of ensuring that inventory items are optimally positioned throughout the supply chain. This includes assessing inventory levels, managing stock turnover, and ensuring that the right products are available at the right time. The goal is to maximize the utility of inventory resources, thereby reducing waste and enhancing productivity.
Importance for Businesses
The importance of inventory activation cannot be overstated. It affects various aspects of a company's performance, from cash flow management to customer satisfaction. Here are some key benefits:
- Cost Efficiency: Effective inventory activation reduces holding costs and minimizes the likelihood of overstocking or stockouts.
- Customer Satisfaction: When inventory is well-activated, businesses can meet customer needs promptly, which enhances overall satisfaction and loyalty.
- Operational Flexibility: A well-activated inventory allows businesses to respond quickly to market changes. This agility can be a significant competitive advantage.
A comprehensive understanding of inventory activation leads to better decision-making and strategic planning for future growth.
By focusing on inventory activation, businesses can create a more efficient and responsive operation. This not only supports the bottom line but also builds a framework for long-term success.
Fundamental Concepts of Inventory Management
Understanding the fundamental concepts of inventory management is essential for any business looking to optimize its operations. Every product line requires a specific strategy to manage stock effectively. This section will lay out the different types of inventory and key metrics. It highlights the considerations every company should keep in mind to maintain operational efficacy.
Inventory Types
Inventory can broadly be classified into three categories: raw materials, work in progress, and finished goods. Each type serves a distinct function in the production and sales process.
Raw Materials
Raw materials are the basic inputs used to create products. Their importance lies in providing the foundation for the entire production process. A key characteristic of raw materials is that they must be carefully sourced and managed to ensure production continuity. This makes them a critical factor for just-in-time (JIT) strategies, which focus on minimizing inventory holding costs.
The unique feature of raw materials is their variability in sourcing. Depending on market conditions, the cost and availability can fluctuate significantly. This poses both advantages and disadvantages. An advantage is the opportunity to negotiate better prices during favorable market conditions. However, the downside is facing supply chain disruptions that could halt production if stock levels are not monitored closely.
Work in Progress
Work in progress (WIP) refers to items that are partially completed but not yet finished goods. WIP serves as an important indicator of a production process's efficiency. A key characteristic of WIP is that it helps in managing production flow and reducing lead times. This is why it is vital for companies aiming to activate inventory.
The unique feature of WIP is that it can be more difficult to value than raw materials or finished goods. Operational efficiency can be affected by how well WIP is managed. If poorly tracked, it can lead to bottlenecks or excess inventory costs. Therefore, it offers both opportunity and risk depending on the effectiveness of inventory management systems in place.
Finished Goods
Finished goods are the completed products ready for sale. Their importance cannot be understated, as they represent the end of the production cycle. A key characteristic of finished goods is their need for accurate forecasting to avoid overstock or stockouts. This category becomes particularly beneficial for businesses with high demand fluctuation.
A unique feature of finished goods is how they are closely linked to customer satisfaction. If the stock level is too low, it can lead to missed sales opportunities. Conversely, having too many finished goods increases carrying costs. Thus, managing this type effectively is critical for profit margins and overall business health.
Key Metrics in Inventory Management
Metrics are vital for a comprehensive understanding of inventory management. They provide the data necessary to make informed decisions.
Turnover Rate
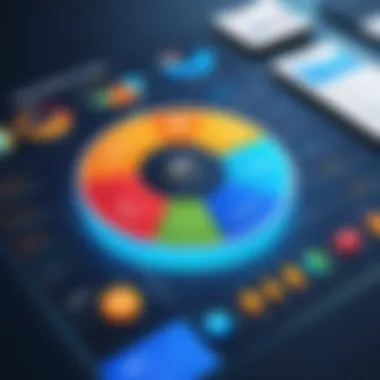
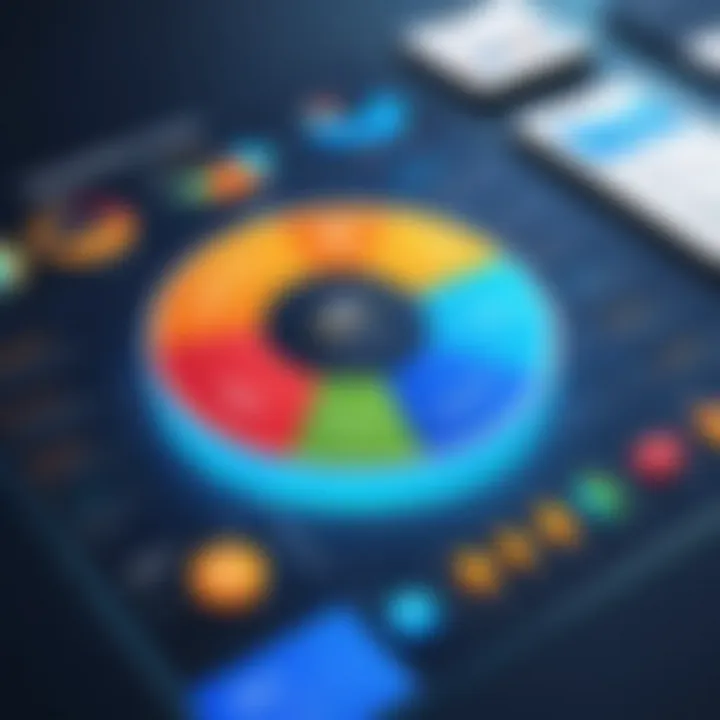
The turnover rate measures how often inventory is sold and replaced over a period. This key metric is crucial for businesses because it indicates the effectiveness of inventory management. A high turnover rate suggests that products are selling quickly, which can lead to improved cash flow.
The unique feature of turnover rate is that it varies by industry. For example, perishables may have a higher turnover compared to durable goods. While a high rate generally signals efficiency, it can also indicate stock shortages if not monitored. Therefore, businesses must find a balance that suits their specific needs.
Stock Levels
Stock levels refer to the quantity of inventory held at any point in time. They are fundamental to ensuring that a business can meet customer demand. A key characteristic of stock levels is that they need to be tracked in real-time to avoid delays in order fulfillment.
The unique feature here is the relationship between stock levels and cash flow. Keeping too low of stock can lead to lost sales, whereas too high can result in unnecessary carrying costs. Regular analytics can help maintain optimal stock levels, ensuring both efficiency and profitability.
Lead Times
Lead times are the total time it takes from placing an order until it is received. This metric is vital for supply chain efficiency. Understanding lead times allows businesses to plan better and align their inventory levels accordingly.
A key characteristic of lead times is that they can vary significantly based on supplier reliability and demand forecasting accuracy. The unique feature here is that shorter lead times can lead to an agile supply chain, enabling faster responses to market changes. However, shorter lead times might require increased costs for expedited shipping.
Effective inventory management requires a deep understanding of various types of inventory and key performance metrics. By mastering these concepts, businesses can better navigate their operational landscapes.
Techniques for Effective Inventory Activation
Effective inventory activation is a cornerstone of operational excellence in businesses today. It involves strategically activating stock to ensure that resources are used efficiently, thereby maximizing profitability. This section outlines three critical techniques that contribute significantly to effective inventory management: Just-In-Time Inventory, ABC Analysis, and Demand Forecasting. Each technique offers unique benefits and considerations that can help businesses navigate their inventory challenges successfully.
Just-In-Time Inventory
Just-In-Time (JIT) inventory is a strategy designed to increase efficiency and decrease waste by receiving goods only as they are needed in the production process. This method reduces the costs associated with holding inventories and minimizes risks tied to overstocking products. It requires precise coordination between suppliers and manufacturing schedules, thus encouraging businesses to build strong relationships with their suppliers.
The advantages of JIT include:
- Reduced Storage Costs: Less inventory means smaller warehouse space is needed.
- Greater Flexibility: Companies can adjust production schedules based on demand without excess inventory.
- Enhanced Quality Control: With less product on hand, businesses can pay more attention to quality.
However, implementing JIT also raises challenges. If a supplier fails to deliver on time, production can halt, leading to missed deadlines and customer dissatisfaction. Therefore, careful planning and reliable partnerships are essential for effective JIT implementation.
ABC Analysis
ABC Analysis is a categorization technique that prioritizes inventory items based on their importance. This method divides inventory into three categories:
- A items (high-value items with low quantity)
- B items (moderate value and quantity)
- C items (low-value items that are abundant)
This analysis allows businesses to focus efforts and resources where they matter most, enabling more effective inventory management. A items receive the highest priority due to their impact on overall profits, while C items require less oversight.
Benefits of ABC Analysis are:
- Optimized Resource Allocation: More attention and resources can be directed toward A items.
- Informed Decision Making: Helps businesses to understand which items contribute most to revenue.
- Efficient Stock Management: Improves inventory turnover ratios by encouraging timely replenishment of high-priority items.
Implementing ABC Analysis is straightforward and can provide instant clarity on inventory status. However, ongoing evaluation is necessary to adjust categories as market conditions change.
Demand Forecasting
Demand forecasting is the process of estimating future customer demand for a product based on historical data and market trends. Accurate demand forecasting can significantly enhance inventory activation efforts by ensuring that stock levels align with anticipated sales.
Incorporating different data sources, such as sales history, market trends, and seasonality, enables businesses to make informed decisions regarding stock levels and purchasing.
Key benefits of effective demand forecasting include:
- Improved Inventory Turnover: Helps reduce excess inventory by aligning supply closely with demand.
- Better Customer Satisfaction: Ensures products are available when customers need them, which can enhance loyalty.
- Reduced Costs: Minimizes the storage costs associated with holding excess inventory.
As with other techniques, demand forecasting faces challenges, particularly in accuracy. External factors such as economic fluctuations and changes in consumer preferences can impact demand unpredictably. Continuous refinement of forecasting methods and tools is essential for maintaining accuracy and reliability.
The Role of Technology in Activating Inventory
Technology plays a critical role in the activation of inventory. It enables businesses to optimize their stock levels through improved processes and data analytics. The integration of technology in inventory management helps in making informed decisions which ultimately enhance operational efficiency. Furthermore, it allows organizations to respond quickly to market changes, reducing the risks associated with overstocking or stockouts. In this landscape, various tools emerge as essential for maintaining the efficacy of inventory workflows.
Inventory Management Software
Inventory management software serves as an essential tool for businesses looking to activate their inventory effectively. These programs provide a centralized platform for tracking stock levels, sales data, and supplier information. With features such as forecasting, reporting, and analytics, this software helps businesses make timely decisions. By organizations utilizing software like Oracle NetSuite, Zoho Inventory, or Fishbowl, they gain better visibility over their stock. This visibility ensures that they do not hold excess inventory while also avoiding situations where they run out of crucial items.
Key benefits of using inventory management software include:
- Streamlined workflows
- Enhanced reporting capabilities
- Improved accuracy in stock counts
Automation Tools
Automation tools are another cornerstone in activating inventory. They reduce the manual effort associated with inventory tasks, allowing teams to focus on more strategic initiatives. Automating processes like order fulfillment, restocking alerts, and inventory counts minimizes human error and increases efficiency. For instance, AutoInventory or TradeGecko can automatically reorder stock based on predefined thresholds. This proactive approach helps maintain optimal inventory levels and ensures that products are available when needed.
Considerations when implementing automation tools include:
- Compatibility with existing systems
- Training for staff to adapt to new technologies
Real-Time Data Tracking
Real-time data tracking is a fundamental aspect of modern inventory management. This technology allows businesses to monitor stock levels, sales, and other key metrics instantaneously. Solutions such as RFID (Radio Frequency Identification) or barcoding systems enable businesses to gain immediate insights into their inventory status, reducing the uncertainty that often accompanies traditional inventory methods.
The implications of real-time data tracking are significant, including:
- Faster response to demand fluctuations
- Improved accuracy in data reporting
- Enhanced customer service by ensuring products are available when required
"Real-time data enables businesses to be agile in their inventory management and respond swiftly to change."
Challenges in Inventory Activation
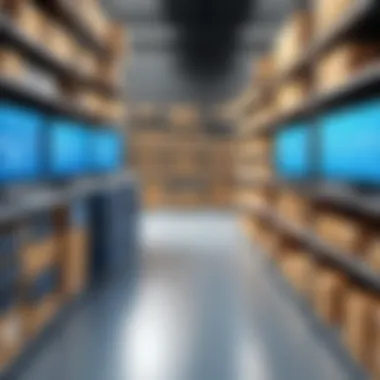
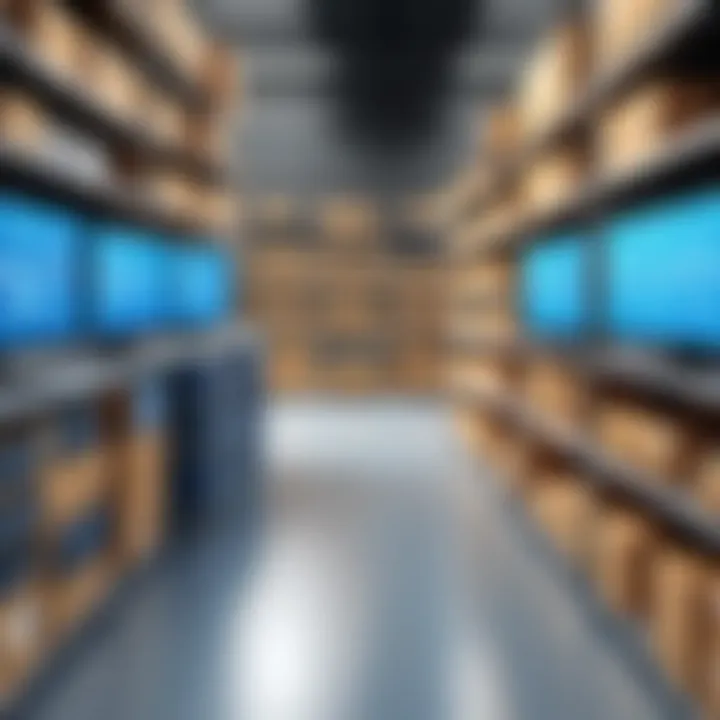
In the complex realm of inventory management, activating inventory presents a variety of challenges that can hinder a business's efficiency and profitability. Recognizing and addressing these challenges is crucial for achieving optimal inventory performance. The significant obstacles include overstock issues, stockouts, and data management complexity. Each of these presents unique difficulties that require careful attention and innovation. Properly addressing these issues can lead to improved inventory flow, reduced costs, and better service to customers.
Overstock Issues
Overstocking can lead to significant financial burdens for businesses. When inventory levels exceed demand, companies may incur unnecessary costs related to storage, insurance, and spoilage. Overstocked items also tie up capital that could be better utilized elsewhere. Regular analysis of sales trends and consumer behavior can help mitigate overstock issues.
Key aspects to consider include:
- Inventory Turnover: A higher turnover rate indicates effective inventory management.
- Demand Forecasting: Accurate forecasting can prevent surplus inventory by aligning stock levels with market needs.
- Clearance Sale Strategies: Implementing measures to sell excess inventory quickly can reduce losses.
Stockouts and Their Implications
Stockouts present another critical challenge. When items are unavailable, customers may turn to competitors, resulting in lost sales and damaged reputation. Stockouts not only affect immediate sales but can also impact long-term customer loyalty.
Mitigating stockouts involves:
- Effective Demand Planning: Utilize historical data to predict future sales.
- Safety Stock: Maintaining a buffer stock can cushion against unexpected demand spikes.
- Supplier Collaboration: Strong relationships with suppliers can lead to quicker replenishment times.
"The balance between overstock and stockouts is delicate; finding the right point is vital for business success."
Data Management Complexity
The increasing volume of inventory data can become overwhelming. Poor data management can lead to discrepancies, inaccuracies, and ultimately poor inventory decisions. Managing data requires robust systems that integrate real-time insights, inventory levels, and sales patterns.
To simplify data management, businesses can:
- Invest in Inventory Management Software: Tools like TradeGecko or NetSuite help streamline processes.
- Utilize Automation: Automating data entry and tracking can minimize human error.
- Regular Reviews and Updates: Consistently auditing data ensures accuracy and relevancy.
These challenges are critical considerations in the process of activating inventory. By confronting these issues, businesses can enhance their operational efficiency and maintain a competitive edge in the market.
Best Practices for Maintaining an Active Inventory
To manage inventory effectively, best practices are essential. These practices not only aid in maximizing the use of resources but also in aligning inventory levels with demand. The ability to maintain an active inventory contributes significantly to operational efficiency. Businesses that employ robust strategies see benefits in various forms, including reduced costs, improved service levels, and enhanced decision-making.
Regular Audits
Regular audits play a crucial role in maintaining accurate inventory records. They involve a systematic review of inventory levels, processes, and practices. The frequency of these audits can vary depending on the size of the business and the volume of stock. For many organizations, a monthly or quarterly audit is sufficient.
Performing audits helps identify discrepancies between physical inventory and recorded amounts. This process not only prevents stockouts but also reduces the risk of overstock situations. Additionally, audits can uncover outdated or non-moving items, which can tie up valuable resources.
The implementation of audit technology, such as barcode scanners and inventory management software, can streamline this process, making it more efficient and less prone to human error. Regular audits foster a culture of accountability, where employees understand the importance of accurate stock management.
Supplier Relationships
Strong supplier relationships are a cornerstone of effective inventory management. These partnerships ensure a consistent supply of materials and products. When businesses cultivate good relationships with suppliers, they can negotiate better terms and gain quicker access to essential inventory.
Having a reliable supplier can also impact lead times. When suppliers are responsive, they can reduce the time between ordering and receiving goods, allowing businesses to maintain optimal stock levels. In times of unexpected demand spikes, a good supplier can provide flexibility, helping businesses adapt swiftly.
Furthermore, keeping an open line of communication with suppliers about forecasted inventory needs can lead to proactive adjustments in supply, minimizing the risk of stock shortages or excess inventory.
Inventory Turnover Optimization
Optimizing inventory turnover is vital to the health of a business. High turnover rates indicate efficient inventory management, as products are sold quickly and replaced, decreasing holding costs. Conversely, low turnover can signal overstock, which can lead to lost revenues and increased carrying costs.
To achieve optimal turnover rates, businesses should implement demand forecasting methods. Understanding customer purchasing patterns can help align inventory with the expected demand. In addition, using techniques such as ABC analysis can also aid in prioritizing high-turnover items.
Another method is to establish clear reorder points for products. Knowing when to reorder ensures that inventory levels remain consistent with market demand, thus preventing stockouts or overstock situations. Regularly reviewing turnover metrics can offer insights into performance, allowing businesses to refine their inventory strategies effectively.
In summary, maintaining an active inventory is a disciplined process that encompasses regular audits, nurturing supplier relationships, and optimizing turnover. By adhering to these best practices, businesses can enjoy improved operational efficiency and responsiveness to market demands.
Analyzing Performance Through KPIs
In the realm of inventory management, analyzing performance through Key Performance Indicators (KPIs) is a cornerstone for success. KPIs provide quantifiable measurements that allow businesses to gauge their operational effectiveness, make informed decisions, and strategize for future improvements. Understanding how well inventory activation is performing can lead to insights that drive efficiency, minimize costs, and enhance customer satisfaction.
Performance analysis through KPIs serves several critical functions:
- Identifying strengths and weaknesses in inventory processes.
- Facilitating data-driven decisions that impact overall business strategy.
- Enhancing alignment between inventory management and broader business goals.
These indicators allow businesses to track their performance over time, enabling adaptations in practices that can significantly influence the bottom line.
Inventory Accuracy Rate
The inventory accuracy rate is a vital KPI that measures how closely a business's recorded inventory matches its actual inventory on hand. A high accuracy rate indicates that businesses effectively manage their stock levels, which is imperative to prevent stockouts and overstock situations.
To improve this metric, organizations need to ensure rigorous auditing practices and employ technologies like barcode scanning and RFID tracking. Regular cycle counts and physical inventory checks help maintain this accuracy.
Benefits of high inventory accuracy include:
- Improved order fulfillment rates.
- Reduced costs associated with overstocking and stockouts.
- Enhanced customer trust by ensuring product availability.
Carrying Cost of Inventory
The carrying cost of inventory reflects the total cost associated with storing unsold goods. This metric encompasses various expenses, including warehousing, insurance, depreciation, and opportunity costs. Understanding these costs is essential for making decisions regarding purchasing and storage strategies.
By calculating carrying costs, businesses gain insights into potential savings and can better assess their inventory policies. Reducing these costs can significantly enhance profitability.
- Strategies to lower carrying costs include:


- Optimizing stock levels based on demand forecasting.
- Implementing just-in-time inventory systems to reduce excess stock.
- Negotiating better terms with suppliers to manage costs more efficiently.
Order Fulfillment Rates
Order fulfillment rates indicate the efficiency with which a business processes customer orders. This KPI measures the percentage of orders shipped accurately and on time. A high order fulfillment rate is indicative of a well-managed inventory system, ensuring that customers receive their products safely and promptly.
The importance of this metric cannot be overstated, as customer satisfaction is heavily influenced by timely delivery. Low fulfillment rates can lead to lost sales and damage a companyโs reputation.
- To improve order fulfillment rates:
- Utilize inventory management systems for better tracking.
- Prioritize training staff on order processing protocols.
- Regularly review and adjust inventory based on sales trends.
Understanding and tracking these KPIs is crucial for businesses aiming to optimize their inventory activation. By focusing on inventory accuracy, carrying costs, and order fulfillment rates, companies can significantly enhance their operational performance.
Advantages of Activating Inventory
Activating inventory plays a pivotal role in the contemporary landscape of business operations. Optimizing stock levels is not merely a strategy to reduce holding costs but also a significant factor influencing overall productivity and customer satisfaction. Companies can reap multiple benefits when they focus on effective inventory activation. Understanding these advantages is essential for business leaders, software developers, and IT professionals who strive for operational excellence.
Increased Efficiency
One of the foremost advantages of activating inventory is the enhancement of operational efficiency. By employing effective inventory activation techniques, businesses can reduce idle stock and streamline their supply chain processes. For instance, implementing Just-In-Time (JIT) inventory practices allows companies to receive goods only as they are needed. This minimizes storage costs while ensuring sufficient stock to meet customer demand.
Furthermore, organizations that actively manage their inventory often find that they can respond to market changes quickly. This agility allows them to adjust to fluctuations in demand without overcommitting resources. As a result, teams can redirect their focus toward enhancing productivity and creativity, rather than grappling with operational bottlenecks.
Cost Reduction
Cost reduction is another crucial advantage tied to activating inventory. High inventory levels lead to increased carrying costs, which include warehousing, insurance, and spoilage. By optimizing inventory, businesses can significantly lower these expenses.
Additionally, vendors such as SAP and Oracle offer advanced analytics tools that help firms monitor and control their inventory more effectively. With real-time data on stock levels and turnover rates, managers can make informed decisions. They can identify slow-moving items to reduce excess stock and improve cash flow.
Consequently, businesses that focus on activating inventory often notice a more lean approach to their costing, leading to higher profitability over time.
Enhanced Customer Satisfaction
Finally, activating inventory directly impacts customer satisfaction. Customers today expect swift delivery and availability of products. By maintaining optimal stock levels, companies can fulfill orders promptly, thereby increasing buyersโ trust and loyalty.
A satisfied customer is more likely to return. They often share their positive experiences through word of mouth or social media. This free marketing is invaluable. According to statistical insights, 79% of customers who are dissatisfied will share their negative experiences with others. Therefore, enhancing inventory activation is a strategic move to improve customer relations.
"Optimizing your inventory is not just about what you keep in stock; itโs about how well you can meet your customerโs needs and expectations."
Engaging in ongoing evaluation and improvement in inventory strategies is beneficial. It ensures that businesses remain agile and responsive to both market demands and customer desires.
Future Trends in Inventory Activation
Understanding future trends in inventory activation is essential for businesses aiming to adapt to a rapidly changing supply landscape. As technology evolves, the methods used for managing and activating inventory must also shift. Organizations that recognize and incorporate these trends stand to gain significant advantages. This section explores two pivotal trends: Artificial Intelligence and Machine Learning, and Blockchain Technology in Supply Chains.
Artificial Intelligence and Machine Learning
Artificial Intelligence (AI) and Machine Learning (ML) are transforming how businesses manage their inventory. By analyzing vast amounts of data, AI can predict trends and demand patterns with high accuracy. This leads to more informed decision-making about stock levels and ordering processes.
The adoption of AI can automate routine tasks, thus reducing human error. For example, AI algorithms can optimize reorder points, ensuring stock levels are maintained without excess. Additionally, it can identify slow-moving inventory that may need markdowns or promotions, helping businesses make proactive decisions that enhance cash flow.
Moreover, Machine Learning can learn from past data, adapting its predictions over time. This continuous learning allows companies to stay ahead of market changes and consumer preferences, ensuring effective inventory activation.
Benefits of AI and in Inventory Activation:
- Improved accuracy in demand forecasting
- Automation of routine inventory tasks
- Increased responsiveness to market changes
- Optimized stock levels, reducing carrying costs
Blockchain Technology in Supply Chains
Blockchain technology is also making significant strides in supply chain management. The core advantage of blockchain is its ability to provide a transparent and immutable ledger of all transactions related to inventory. This enhances trust between parties involved in the supply chain.
By utilizing blockchain, companies can track the provenance of goods through every stage of the supply chain. This capability improves accountability and reduces the risk of fraud. Additionally, it facilitates more efficient inventory audits, as verifiable data is readily available.
Another critical aspect of blockchain is its potential to streamline communication among suppliers, manufacturers, and retailers. This transparency can help in faster decision-making regarding inventory levels, reducing overstock situations and stockouts.
Considerations for Implementation of Blockchain:
- Integration with existing systems and processes
- Education of stakeholders involved in supply chains
- Consideration of regulatory implications
"Adapting to new technologies in inventory management is not just a competitive advantage but a necessity in todayโs market."
Embracing AI and blockchain technology presents lucrative opportunities for enhancing inventory activation. Companies that effectively leverage these technologies will improve their operational efficiency and align better with consumer demands.
Culmination
The conclusion serves as a crucial component of this article, providing a summation of the main ideas discussed throughout. It allows readers to consolidate their understanding of inventory activation, a multifaceted topic with significant implications for businesses.
Recap of Key Concepts
In this article, we have covered several essential aspects of activating inventory:
- Understanding Inventory Activation: Defined the process and its importance in optimizing stock levels.
- Fundamental Concepts: Explored different inventory types and key metrics.
- Techniques: Highlighted effective strategies including Just-In-Time and Demand Forecasting.
- Role of Technology: Discussed how software and automation tools aid inventory management.
- Challenges: Identified common problems like overstock and data management complexities.
- Best Practices: Suggested methods for maintaining active inventory through audits and supplier relationships.
- Performance Analysis: Analyzed important KPIs to measure effectiveness.
- Advantages: Covered the benefits of efficiently activating inventory, such as increased efficiency and customer satisfaction.
- Future Trends: Examined emerging technologies like AI and blockchain that may influence inventory practices.
This recap highlights not just the diversity of topics covered, but also the interconnections between them, reinforcing the notion that effective inventory management requires a holistic approach.
Final Thoughts on Inventory Activation
As we move toward an increasingly digitalized business environment, activating inventory emerges as an imperative strategy for growth. Companies must adapt to changing consumer demands while managing their stock efficiently. Understanding key concepts, metrics, and innovative tools empowers organizations to make better decisions about inventory levels.
Key considerations include:
- The necessity of integrating advanced technology to streamline processes.
- The importance of regular audits and performance assessments to maintain accuracy.
- Building strong relationships with suppliers to ensure a steady flow of inventory.
Overall, inventory activation should be viewed as a dynamic practice that evolves with market trends and business needs. It is not a one-time effort but an ongoing journey that contributes to overall business success.